Unraveling About Aluminum Casting: From Fundamentals to Know-how
Unraveling About Aluminum Casting: From Fundamentals to Know-how
Blog Article
Unlocking the Possible of Light Weight Aluminum Casting: Proven Strategies for Success
Light weight aluminum spreading has long been recognized for its versatility and prevalent applications across various sectors - about aluminum casting. Revealing the full capacity of this procedure needs more than simply fundamental knowledge. By applying tried and tested approaches sharpened via years of market experience and technology, manufacturers can elevate their light weight aluminum casting procedures to new elevations of performance and high quality. From maximizing style factors to consider to enhancing manufacturing processes, the vital lies in using these techniques properly. Join us as we check out the essential aspects that can propel light weight aluminum spreading towards unmatched success in today's open market landscape.
Advantages of Light Weight Aluminum Spreading
Light weight aluminum spreading offers a wide range of benefits that make it a recommended selection in various commercial applications. Among the primary benefits of aluminum casting is its lightweight nature, which adds to sustain effectiveness in sectors such as auto and aerospace. Additionally, aluminum is highly malleable, permitting elaborate and complicated forms to be quickly created with casting processes. This adaptability in style is a substantial benefit for markets that need elements with certain geometries.
Moreover, light weight aluminum spreading supplies excellent deterioration resistance, making it optimal for applications where exposure to rough settings is an issue. The product also exhibits excellent thermal conductivity, which is advantageous for industries needing warm dissipation, such as electronics (about aluminum casting). Light weight aluminum is fully recyclable, straightening with the growing focus on sustainable techniques in contemporary manufacturing.
Style Considerations for Casting
When taking into consideration casting style, meticulous interest to detail is vital to guarantee the effective production of high-grade elements. The layout phase plays a critical function in the overall success of a light weight aluminum spreading project. One vital consideration is the choice of appropriate geometries and functions that facilitate the casting procedure. Developers should take into consideration factors such as draft angles, fillets, and wall surface density to ensure appropriate steel flow and solidification during spreading.
Furthermore, considerations associated to parting lines, gating systems, and risers are important to prevent problems like porosity and shrinking. It is critical to optimize the design for efficient material usage and lessen post-processing needs. Simulations and prototyping can be beneficial devices in evaluating and refining the casting layout prior to major manufacturing.
Cooperation in between layout manufacturers, engineers, and factories is crucial to resolve any type of prospective challenges early in the layout phase. By incorporating these considerations right into the spreading design process, makers can boost product high quality, minimize expenses, and ultimately open the complete capacity of aluminum spreading.
Enhancing Casting Effectiveness
When intending to improve casting performance in aluminum spreading projects,Creating with a focus on enhancing product flow and decreasing problems is crucial. To accomplish this, making use of simulation software application can assist in identifying prospective concerns before the spreading procedure begins. By replicating the flow of molten light weight aluminum, designers can change gating and riser layouts to ensure appropriate dental filling and solidification, ultimately minimizing the event of defects such as porosity or shrinking.
In addition, executing appropriate warmth treatment processes can improve the total casting efficiency. Warm therapy can aid improve the mechanical properties of the aluminum casting, making sure that the last part meets the required specs. Furthermore, utilizing automation and robotics in the spreading procedure can simplify manufacturing, reduce manual labor, and boost general effectiveness.
Moreover, continual surveillance and top quality control during the spreading procedure are critical for determining any kind of inconsistencies and guaranteeing that the end products fulfill the desired requirements. By applying these strategies, makers can improve casting effectiveness, enhance product quality, and ultimately achieve greater success in light weight aluminum spreading jobs.
High Quality Control in Aluminum Casting
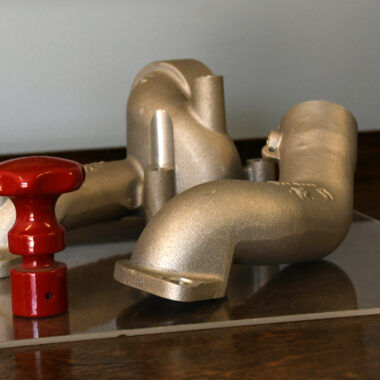
Efficient top quality control techniques play a crucial duty in making certain the accuracy and integrity of light weight aluminum spreading processes. Quality control steps in aluminum casting incorporate an array of tasks intended at supporting particular standards and identifying deviations that can go to website endanger the last product.
Along with procedure control, quality assurance in light weight aluminum casting involves strenuous screening and evaluation procedures at numerous phases of production. Non-destructive testing approaches like ultrasonic testing and X-ray evaluation aid identify interior problems without compromising the honesty click of the cast components. Aesthetic evaluations, dimensional measurements, and mechanical screening even more ensure that the actors parts fulfill the needed specifications and efficiency requirements. By implementing durable quality control techniques, aluminum spreading facilities can supply products that fulfill client assumptions for high quality, reliability, and performance.
Maximizing Success
To accomplish optimum economic efficiency, a comprehensive technique for optimizing productivity within light weight aluminum spreading procedures must be meticulously devised and carried out. One crucial aspect of making the most of profitability in aluminum casting is enhancing production performance. This involves simplifying procedures, lowering waste, and reducing downtime to guarantee that resources are utilized efficiently. Carrying out lean production principles can assist identify locations for improvement and boost overall functional effectiveness.
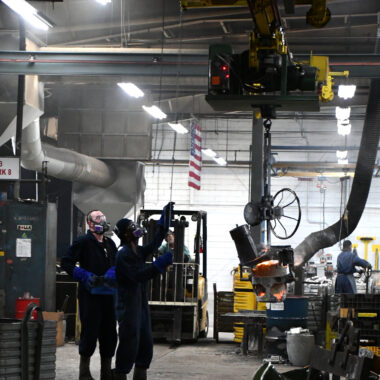
Furthermore, diversifying product offerings and exploring new markets can aid increase earnings streams. Recognizing consumer demands and market patterns can assist calculated decisions to take advantage of emerging opportunities. Purchasing research and growth to introduce processes or items can likewise drive earnings with differentiation and consumer satisfaction.
Verdict
Finally, aluminum casting supplies countless advantages in terms of layout flexibility, durability, and cost-effectiveness. By very carefully considering layout considerations, boosting casting effectiveness, implementing top quality control steps, and maximizing earnings, producers Full Report can open the full capacity of aluminum casting. This reliable and flexible procedure has verified to be a successful selection for a wide variety of commercial applications.
Furthermore, light weight aluminum is very flexible, enabling for intricate and complicated forms to be conveniently produced with spreading procedures.Efficient high quality control techniques play a pivotal function in making sure the accuracy and reliability of aluminum spreading procedures.In enhancement to process control, quality control in aluminum spreading entails strenuous testing and evaluation procedures at different phases of manufacturing. By implementing robust quality control methods, aluminum spreading centers can supply items that fulfill consumer assumptions for reliability, performance, and quality.
By carefully considering design factors to consider, boosting casting performance, applying top quality control procedures, and making best use of productivity, suppliers can open the complete capacity of aluminum spreading.
Report this page